Welcome to our comprehensive guide on understanding the key chemicals used to harden concrete. Whether you’re a construction professional, a DIY enthusiast, or simply curious about the materials that shape our world, this blog is designed to provide you with valuable insights. Concrete is an essential material in construction, and the process of hardening is crucial to its strength and durability. In this article, we’ll delve into the basics of concrete, the hardening process, and the specific chemicals involved. By the end, you’ll have a clear understanding of how these chemicals work and why they’re vital to the integrity of concrete structures. Let’s explore the fascinating world of concrete hardening together!
The primary chemical used to harden concrete is Calcium Silicate Hydrate (CSH), formed through the hydration reaction between cement and water. This process is essential for the strength and durability of concrete. Additionally, accelerators like Calcium Chloride can be used to speed up the hardening process, while retarders and other admixtures help modify concrete properties for various construction needs.
Table of Contents
Basics Of Concrete
Definition: What is Concrete?
Concrete is a versatile and essential building material used globally in various construction projects, from sidewalks to skyscrapers. It’s a composite material, meaning it combines multiple substances to form a single, robust product. Essentially, concrete is a mix of cement, water, and aggregates (like sand, gravel, or crushed stone), which hardens over time to create a stone-like material. The adaptability and strength of concrete make it a popular choice for many construction applications, providing durability and resilience to structures.
Components of Concrete
Concrete’s effectiveness and reliability come from its three primary components, each playing a crucial role in the final product:
- Cement: Cement acts as the binder in concrete, holding everything together. The most common type used is Portland cement, which is made by heating limestone and clay to high temperatures. Once mixed with water, cement undergoes a chemical reaction called hydration, forming a paste that coats the aggregates and hardens over time.
- Water: Water is essential for the hydration process, allowing the cement to activate and bind the aggregates. The amount of water used in the mix is crucial; too much water can weaken the concrete, while too little can prevent proper hydration, leading to a brittle mixture.
- Aggregates: Aggregates make up the bulk of the concrete mixture, providing compressive strength and bulk. They come in various sizes, from fine particles like sand to larger chunks like gravel or crushed stone. The choice of aggregates affects the concrete’s strength, durability, and overall performance.
The Process of Making Concrete
Creating concrete involves a straightforward yet precise process to ensure the final product meets the desired specifications. Here’s a basic overview:
1. Mixing: The components – cement, water, and aggregates – are measured and combined. The proportions depend on the specific requirements of the project, such as the needed strength and durability.
2. Hydration: Once mixed, the water and cement undergo hydration, forming a gel-like paste that starts binding the aggregates. This chemical reaction generates heat and continues over time, contributing to the hardening process.
3. Pouring: The fresh concrete mix is then poured into molds or forms. It’s essential to work quickly and efficiently to prevent the concrete from setting too early during this stage.
4. Curing: After pouring, concrete needs time to cure, which involves maintaining adequate moisture and temperature conditions. Proper curing is vital as it ensures the concrete reaches its maximum strength and durability. The curing process can take several days to weeks, depending on the type of concrete and environmental conditions.
Importance of Hardening
The hardening process is critical for concrete’s performance and longevity. As concrete cures, it gradually gains strength and becomes more resistant to environmental factors like weather changes, chemical exposure, and physical wear. This transformation from a pliable mix to a solid, stone-like material is what gives concrete its renowned durability and versatility. Ensuring proper hardening through adequate curing practices is essential for any construction project, as it directly impacts the structural integrity and lifespan of the finished product.
By understanding the basics of concrete – from its definition and components to the making and hardening process – one can appreciate why this material is fundamental to modern construction. Its unique properties and adaptability continue to make concrete a cornerstone of the building industry.

The Hardening Process Of Concrete
Concrete hardening is a fascinating process that begins the moment water comes into contact with cement. This transformation, known as the hydration process, involves a complex series of chemical reactions that convert the mixture from a pliable paste into a robust, solid structure. Understanding the intricacies of this process can help ensure the successful execution of concrete projects, whether you’re building a driveway, a foundation, or any other structure.
Chemical Reaction
The hardening of concrete starts with hydration, a crucial chemical reaction that occurs when water is added to cement. This process involves the dissolution of cement particles, which then react with water to form various hydration products. These products gradually crystallize and interlock, creating a hardened matrix that binds the aggregates together.
The primary hydration product is calcium silicate hydrate (C-S-H), which is responsible for the strength and durability of concrete. Another significant product is calcium hydroxide, which contributes to the pH of the concrete and helps protect the embedded steel reinforcement from corrosion. The hydration process generates heat, known as the heat of hydration, which can influence the rate at which concrete hardens and gains strength.
Stages of Hardening
The hardening process of concrete is divided into two main stages: the initial set and the final set.
1. Initial Set
The initial set occurs relatively quickly after the mixing process begins. During this stage, the concrete starts to lose its plasticity and becomes firm enough to hold its shape. The time it takes for concrete to reach its initial set can vary but typically occurs within the first few hours. It’s crucial to complete any necessary finishing operations, such as troweling or smoothing, before the concrete reaches this stage.
2. Final Set
The final set is the point at which the concrete has hardened to the extent that it can support some weight and resist minor pressures. This stage marks the end of the setting period and the beginning of the hardening phase. The final set typically occurs within 24 to 48 hours after mixing, but the concrete will continue to gain strength over time. During this period, it’s essential to ensure proper curing conditions to promote optimal hydration and strength development.
Factors Affecting Hardening
Several factors can influence the rate and effectiveness of the concrete hardening process. These include temperature, moisture levels, and mix ratios.
1. Temperature
Temperature plays a significant role in the rate of hydration and the overall hardening process. Warmer temperatures accelerate the chemical reactions, leading to a faster initial set and final set. However, if the temperature is too high, it can cause rapid evaporation of water, potentially leading to cracking and reduced strength. Conversely, colder temperatures slow down the hydration process, delaying the hardening and strength gain. In extreme cases, freezing temperatures can halt hydration altogether, resulting in weak, compromised concrete.
2. Moisture Levels
Adequate moisture is essential for the hydration process. If the concrete dries out too quickly, the hydration reaction can be incomplete, leading to a weaker final product. Maintaining proper moisture levels through curing methods, such as water spraying, covering with wet burlap, or using curing compounds, helps ensure continuous hydration and strength development. On the other hand, excessive moisture can lead to waterlogging, affecting the concrete’s structural integrity and leading to problems like scaling and reduced durability.
3. Mix Ratios
The proportions of cement, water, and aggregates in the concrete mix significantly impact the hardening process. The water-cement ratio, in particular, is critical. Too much water can result in a diluted cement paste, reducing the concrete’s strength and durability. Too little water can make the mix difficult to work with and lead to incomplete hydration. Achieving the right balance ensures a workable mix that hardens into a strong, durable concrete structure. Additionally, the quality and gradation of aggregates can affect the mix’s consistency and the final product’s strength and stability.
Understanding these aspects of the hardening process allows for better planning and execution of concrete projects, ensuring the final structure meets the desired strength and durability requirements. Whether you’re a contractor, builder, or DIY enthusiast, knowledge of concrete hardening is essential for successful construction.
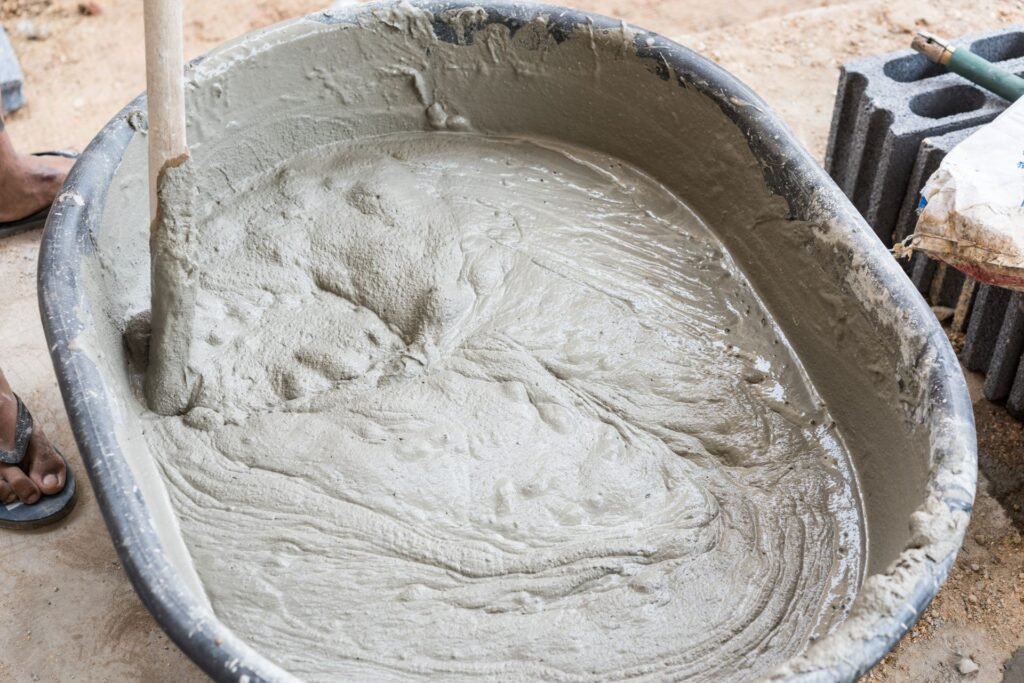
Chemicals Used To Harden Concrete
When it comes to hardening concrete, various chemicals play pivotal roles in ensuring the material achieves the desired strength and durability. This section delves into the primary chemical involved in the hardening process, as well as accelerators, retarders, and other admixtures that are commonly used to modify the properties of concrete.
Primary Chemical: Calcium Silicate Hydrate (CSH)
The backbone of concrete hardening is Calcium Silicate Hydrate (CSH), the primary product of hydration. When cement reacts with water, CSH is formed, which gives concrete its strength and structure. This reaction is fundamental to the concrete hardening process, making CSH an essential component in any concrete mix.
Accelerators: Speeding Up the Hardening Process
Accelerators are chemicals that expedite the hardening process of concrete. One of the most commonly used accelerators is Calcium Chloride.
Usage: Accelerators are particularly useful in cold weather conditions where the setting time of concrete is slowed down due to lower temperatures. By speeding up the hardening process, accelerators ensure that construction projects can proceed on schedule, even in less-than-ideal weather conditions.
Pros and Cons:
- Pros: Accelerators can significantly reduce the setting time, which is beneficial for fast-track construction projects. They can also improve early strength development, which is crucial for early formwork removal and load application.
- Cons: The use of accelerators, particularly Calcium Chloride, can lead to potential corrosion of steel reinforcement if not used correctly. It can also cause a reduction in long-term strength if overused.
Retarders: Slowing Down the Hardening Process
Retarders are chemicals that slow down the hardening process of concrete. Common retarders include sugars and certain acids.
Usage: Retarders are beneficial in hot weather conditions where concrete might set too quickly. They allow for more workable time, which is essential for complex pours and finishes. They are also used in situations where extended transportation time is required for the concrete mix.
Pros and Cons:
- Pros: Retarders provide more time for the placement and finishing of concrete, ensuring a high-quality finish. They also help in reducing the risk of cold joints in large pours.
- Cons: If not used correctly, retarders can overly delay the setting time, which can interfere with construction schedules. Over-retardation can also negatively impact the long-term strength of the concrete.
Admixtures: Modifying Concrete Properties
Besides accelerators and retarders, other admixtures are commonly used to enhance or modify the properties of concrete. Some of the notable ones include Superplasticizers and Air-entraining agents.
Types and Functions
- Superplasticizers: These are high-range water reducers that allow for a significant reduction in water content while maintaining workability. They are used to produce high-strength concrete and improve its flow properties.
- Air-entraining Agents: These admixtures introduce tiny air bubbles into the concrete mix, which enhances its resistance to freeze-thaw cycles. This is particularly important in regions with harsh winters.
- Functions: Admixtures can improve the workability, durability, and overall performance of concrete. They can also be used to address specific challenges, such as reducing shrinkage, improving pumpability, and enhancing the finish quality.
In conclusion, the use of various chemicals in concrete is essential for achieving the desired properties and performance. Understanding the roles of Calcium Silicate Hydrate, accelerators, retarders, and other admixtures allows for the optimization of concrete for different construction needs and environmental conditions.

Practical Applications And Case Studies
Construction Industry
Concrete hardening chemicals play a crucial role in the construction industry, particularly in large-scale projects where time and efficiency are paramount. These chemicals, such as accelerators and retarders, are used to modify the setting and hardening rates of concrete to meet specific project requirements. For instance, accelerators are often added to the concrete mix to speed up the curing process, allowing construction to proceed more quickly, especially in colder climates where concrete naturally takes longer to set. This can be essential for projects with tight deadlines, such as bridges, skyscrapers, and infrastructure developments.
Retarders, on the other hand, are used to delay the setting time of concrete. This is particularly useful in hot weather conditions where concrete can set too quickly, potentially leading to cracks and structural weaknesses. By extending the setting time, retarders allow for longer working times, ensuring the concrete is properly placed and finished before it hardens.
DIY Projects
For home improvement enthusiasts, concrete hardening chemicals can also be highly beneficial. Whether you’re working on a patio, driveway, or garden pathway, understanding how to use these chemicals can greatly enhance the quality and durability of your DIY projects. Here are a few practical tips:
1. Choose the Right Chemical: Select an accelerator or retarder based on the weather conditions and the specific needs of your project. For colder weather, an accelerator can help ensure your concrete cures properly. In hot weather, a retarder can prevent premature setting.
2. Mixing: Carefully follow the manufacturer’s instructions when adding the chemical to your concrete mix. Proper mixing is crucial to ensure the chemical is evenly distributed.
3. Timing: Pay close attention to the setting time. Accelerators will reduce the time you have to work with the concrete, so be prepared to move quickly. Retarders will give you more time, which can be helpful for more complex projects.
Case Study 1: Successful Use of Accelerators in a High-Rise Building Project
In a recent high-rise building project in a busy metropolitan area, the use of concrete accelerators was a game-changer. The project had a tight deadline, and the construction team needed to pour concrete for the foundations and lower floors during the winter months. By incorporating accelerators into the concrete mix, the team was able to significantly reduce the curing time, allowing for faster progression of the construction schedule.
The accelerators ensured that the concrete reached the necessary strength in a shorter period, which was particularly important for maintaining the structural integrity of the building during the early stages. This approach not only kept the project on schedule but also helped to mitigate the risks associated with cold weather concreting, such as freezing and delayed curing.
Case Study 2: Effective Use of Retarders in a Large-Scale Pavement Project
In another example, a large-scale pavement project in a tropical region faced challenges due to the high temperatures, which caused the concrete to set too quickly. This rapid setting made it difficult for workers to properly place and finish the concrete, leading to surface defects and potential structural issues.
To address this, the construction team decided to use concrete retarders. By adding retarders to the mix, they were able to slow down the setting time, providing more working time to ensure the concrete was correctly placed and finished. This not only improved the quality of the pavement but also reduced the likelihood of cracks and other defects that could compromise the longevity of the pavement.
The use of retarders in this project exemplifies how adjusting the setting time of concrete can lead to better outcomes, especially in challenging environmental conditions. The extended working time allowed for more precise placement and finishing, resulting in a smoother, more durable surface that met the project’s specifications and quality standards.
Understanding the practical applications and benefits of concrete hardening chemicals is essential for both large-scale construction projects and DIY enthusiasts. Whether accelerating or retarding the setting time, these chemicals can significantly impact the efficiency and quality of concrete work. By learning from real-world case studies, we can see the tangible benefits these chemicals bring to diverse construction scenarios.

Safety And Environmental Considerations
Handling Chemicals
When working with chemicals, safety is paramount to protect both yourself and those around you. Here are some essential safety tips for handling and using chemicals effectively:
1. Personal Protective Equipment (PPE): Always wear the appropriate PPE, which includes gloves, goggles, and protective clothing, to prevent direct contact with hazardous substances. In some cases, a respirator may be necessary to avoid inhaling harmful fumes.
2. Proper Storage: Store chemicals in a cool, dry place, away from direct sunlight and sources of ignition. Ensure that they are kept in clearly labeled containers to avoid accidental misuse.
3. Ventilation: Work in well-ventilated areas to prevent the buildup of toxic fumes. If working indoors, use fume hoods or exhaust fans to maintain air quality.
4. Read Labels and Safety Data Sheets (SDS): Before using any chemical, thoroughly read its label and SDS to understand its properties, hazards, and the precautions needed for safe handling.
5. Spill Management: Be prepared for accidental spills by having spill containment kits readily available. Know the correct procedures for cleaning up different types of chemicals to minimize exposure and environmental contamination.
6. Disposal: Dispose of chemicals properly according to local regulations. Never pour them down the drain or into the environment. Instead, use designated disposal containers and facilities.
Environmental Impact
Using chemicals comes with environmental considerations that must be addressed to minimize their impact on ecosystems and human health.
Sustainability Practices
1. Choosing Eco-Friendly Products: Whenever possible, select chemicals that are biodegradable or have a lower environmental footprint. Look for products with certifications indicating their environmental safety.
2. Minimizing Use: Use chemicals sparingly and only in the necessary quantities to reduce waste and pollution. Implementing efficient use practices can significantly cut down on the volume of chemicals released into the environment.
3. Recycling and Reuse: Some chemicals can be recycled or reused safely. Establishing systems for reclaiming and reprocessing chemicals can reduce the need for new products and lessen waste.
4. Proper Disposal: As mentioned earlier, dispose of chemicals according to local environmental regulations to prevent contamination of soil and water sources. Engage with certified waste management services for proper disposal methods.
5. Education and Training: Regularly train employees and stakeholders on the best practices for chemical use and environmental safety. Awareness and education are key to fostering a culture of sustainability.
6. Environmental Monitoring: Implement regular monitoring of air, water, and soil quality around areas where chemicals are used or stored. This helps in early detection of contamination and allows for timely remediation efforts.
By adhering to these safety and environmental practices, we can ensure that the use of chemicals remains responsible and sustainable, protecting both human health and the environment.

Future Trends In Concrete Hardening
Concrete hardening is an evolving field, with new trends and technologies emerging to enhance durability, sustainability, and overall performance. Let’s delve into some key future trends in concrete hardening, highlighting innovative chemicals, sustainable solutions, and ongoing research and development.
Innovative Chemicals
The construction industry is witnessing a surge in the development of innovative chemicals designed to improve concrete hardening. These chemicals aim to enhance the material’s strength, reduce curing time, and increase its resistance to environmental factors.
1. Self-Healing Concrete: One of the most groundbreaking innovations is self-healing concrete. This type of concrete incorporates bacteria or other agents that activate when cracks form, effectively “healing” the material and extending its lifespan. This technology not only reduces maintenance costs but also minimizes the need for frequent repairs.
2. Nanotechnology: Nanotechnology is playing a significant role in the development of new hardening agents. By manipulating materials at the molecular level, scientists can create concrete that is stronger, more durable, and more resistant to wear and tear. Nano-silica, for instance, can significantly enhance the compressive strength of concrete.
3. Polymer-Based Admixtures: The use of polymer-based admixtures is another trend gaining traction. These admixtures improve the flexibility and toughness of concrete, making it more adaptable to various construction needs. They also enhance the material’s resistance to chemicals and weathering.
Sustainable Solutions
As the construction industry moves towards more sustainable practices, the development of eco-friendly hardening agents is becoming a priority. These solutions aim to reduce the environmental impact of concrete production and use.
1. Bio-Based Hardeners: Bio-based hardening agents, derived from renewable resources, are emerging as a viable alternative to traditional chemicals. These agents not only reduce the carbon footprint of concrete but also promote a more sustainable construction industry.
2. Recycled Materials: Incorporating recycled materials into concrete hardening processes is another sustainable trend. Using industrial by-products like fly ash, slag, and silica fume can enhance the properties of concrete while reducing waste and conserving natural resources.
3. Low-Carbon Concrete: The development of low-carbon concrete is a critical step towards sustainable construction. By optimizing the mix design and using alternative binders, such as geopolymers, the carbon emissions associated with concrete production can be significantly reduced.
Research and Development
Ongoing research and development are crucial for the continuous improvement of concrete hardening technologies. Universities, research institutions, and industry leaders are collaborating to explore new possibilities and address existing challenges.
1. Advanced Modeling Techniques: Researchers are utilizing advanced modeling techniques to predict the behavior of concrete under various conditions. These models help in optimizing mix designs and improving the performance of hardening agents.
2. Durability Studies: Long-term durability studies are essential for understanding how concrete performs over time. These studies focus on the effects of environmental exposure, load-bearing capacity, and resistance to chemical attacks, providing valuable insights for developing more resilient concrete.
3. Smart Concrete: The concept of smart concrete, which incorporates sensors and monitoring systems, is gaining attention. This technology allows real-time monitoring of concrete conditions, enabling proactive maintenance and reducing the risk of structural failures.
The future of concrete hardening is bright, with numerous innovations and advancements on the horizon. From self-healing concrete and nanotechnology to sustainable solutions and ongoing research, these trends are set to revolutionize the construction industry. By staying abreast of these developments, professionals can leverage new technologies to create stronger, more durable, and environmentally friendly concrete structures.
Incorporating these emerging trends into your projects not only ensures better performance and longevity but also aligns with the global shift toward sustainability in construction. As we look forward, the continued collaboration between researchers, industry leaders, and policymakers will be pivotal in driving these innovations forward, ultimately transforming the way we build and maintain our infrastructure.

FAQs: About What Chemical Is Used To Harden Concrete
What is the primary chemical used to harden concrete?
The primary chemical used to harden concrete is Calcium Silicate Hydrate (CSH), which forms through the hydration reaction between cement and water.
How does Calcium Silicate Hydrate (CSH) contribute to concrete hardening?
CSH forms as a result of the chemical reaction between cement and water, binding the aggregate materials together and providing the concrete with its strength and durability.
What are accelerators, and how do they affect the concrete hardening process?
Accelerators are chemicals, such as Calcium Chloride, added to concrete to speed up the hardening process. They are often used in cold weather conditions or when a quick setting is required.
What are retarders, and why are they used in concrete?
Retarders are chemicals that slow down the hardening process of concrete. They are used in hot weather conditions to prevent premature setting and to allow more time for working with the concrete.
Can using accelerators or retarders affect the final strength of the concrete?
Yes, using accelerators can increase early strength but may slightly reduce long-term strength, while retarders can help maintain workability without compromising the final strength of the concrete.
What other types of admixtures are commonly used in concrete?
Other common admixtures include superplasticizers, which improve workability, and air-entraining agents, which introduce tiny air bubbles to improve freeze-thaw resistance.
Are there any environmental concerns associated with using these chemicals in concrete?
Yes, some chemicals used in concrete can have environmental impacts. It’s important to use them responsibly and consider sustainable alternatives when possible.
How can I safely handle and use chemicals for concrete hardening?
Always follow the manufacturer’s safety guidelines, use appropriate personal protective equipment (PPE), and ensure good ventilation when handling chemicals.
Are there any innovative chemicals or technologies emerging in the field of concrete hardening?
Yes, research is ongoing to develop more eco-friendly and efficient chemicals for concrete hardening, such as alternative binders and nano-materials that enhance performance and sustainability.
Where can I find more information about concrete hardening and the chemicals involved?
For more information, you can consult construction handbooks, and industry standards, or reach out to professional associations in the concrete and construction industry. Additionally, academic journals and online resources provide in-depth studies and updates on this topic.
Conclusion
In conclusion, understanding and using the right chemicals for concrete hardening is crucial for ensuring the durability and longevity of your construction projects. Throughout this discussion, we’ve explored the key factors that influence concrete hardening, the various chemicals available, and their specific benefits. It’s evident that making informed choices in this area can significantly impact the quality and performance of your concrete structures. As you embark on your own projects, consider the insights shared here, and don’t hesitate to experiment and share your experiences. Whether you’re a seasoned professional or a DIY enthusiast, your feedback and questions are invaluable. Feel free to reach out for more information or to share your stories – let’s continue the conversation and enhance our collective knowledge on concrete hardening.
About the Author:
Mike Veail is a recognized digital marketing expert with over 6 years of experience in helping tradespeople and small businesses thrive online. A former quantity surveyor, Mike combines deep industry knowledge with hands-on expertise in SEO and Google Ads. His marketing strategies are tailored to the specific needs of the trades sector, helping businesses increase visibility and generate more leads through proven, ethical methods.
Mike has successfully partnered with numerous companies, establishing a track record of delivering measurable results. His work has been featured across various platforms that showcase his expertise in lead generation and online marketing for the trades sector.
Learn more about Mike's experience and services at https://theleadguy.online or follow him on social media: