Welcome to an enlightening exploration into the world of concrete, where we unravel the crucial science behind the water-cement ratio. This fundamental concept plays a pivotal role in the strength, durability, and overall performance of concrete, a material that forms the backbone of our modern infrastructure. Understanding the water-cement ratio isn’t just for engineers and construction professionals; it’s essential knowledge for anyone interested in the foundations of our built environment. In this blog post, we’ll delve into why this ratio is so critical, how it impacts various aspects of concrete, and what you need to know to ensure the best results in any concrete project. Join us as we demystify the science that keeps our structures standing strong and resilient.
The water-cement ratio is crucial in concrete science because it directly affects the strength, durability, and workability of concrete. A proper balance ensures optimal hydration, leading to a robust and long-lasting structure. Too much water weakens concrete, making it prone to cracks and reduced durability, while too little water hampers workability and strength. Understanding and controlling this ratio is essential for high-quality concrete in construction projects.
Table of Contents
Understanding The Water-Cement Ratio
The water-cement ratio is a crucial concept in the world of concrete construction. It refers to the ratio of the weight of water to the weight of cement used in a concrete mix. This ratio significantly influences the strength and durability of concrete, making it an essential factor in construction projects.
Definition
The water-cement ratio, often abbreviated as the w/c ratio, is a measure used to determine the amount of water relative to the amount of cement in a concrete mix. Essentially, it defines the quantity of water needed for the hydration of cement and provides the workability necessary for the concrete mix to be properly placed and compacted. A lower water-cement ratio leads to higher strength and durability, while a higher ratio results in increased workability but may compromise the structural integrity of the concrete.
Formula
The formula for calculating the water-cement ratio is straightforward. It is expressed as the weight of water divided by the weight of cement:
{Water-Cement Ratio (w/c)} = \frac{Weight of Water}{Weight of Cement}
For instance, if a concrete mix requires 50 kilograms of water and 100 kilograms of cement, the water-cement ratio would be:
{w/c} = \frac{50}{100} = 0.5
This means that there are 0.5 kilograms of water for every kilogram of cement used in the mix.
Historical Context
The concept of the water-cement ratio was first introduced by Duff A. Abrams, a pioneering American engineer, in the early 20th century. Abrams conducted extensive research on the properties of concrete and established the relationship between the water-cement ratio and the strength of concrete. His findings were published in the form of the “Abrams’ Law” or “Abrams’ Water-Cement Ratio Law” in 1918, which fundamentally transformed concrete mix design.
Before Abrams’ research, concrete mix proportions were often based on empirical methods and rule-of-thumb practices, leading to inconsistencies in the quality and performance of concrete structures. Abrams’ work provided a scientific basis for designing concrete mixes, ensuring greater uniformity and predictability in concrete’s behavior.
Over the years, the understanding and application of the water-cement ratio have evolved with advancements in materials science and construction techniques. Modern concrete technology now incorporates various admixtures and supplementary cementitious materials to optimize the water-cement ratio for specific performance requirements, such as high-strength or high-durability concrete.
In summary, the water-cement ratio is a fundamental concept in concrete mix design that directly affects the strength, durability, and workability of concrete. By understanding and controlling this ratio, engineers and construction professionals can create concrete structures that meet specific performance criteria and stand the test of time. The historical development of this concept, spearheaded by Duff A. Abrams, has had a profound impact on the construction industry, paving the way for more reliable and efficient concrete construction practices.

The Role Of Water In Concrete
Water plays a crucial role in the concrete mix, influencing various aspects of the final product’s performance and durability. Understanding the importance of water in concrete can help ensure the creation of strong, long-lasting structures. Let’s explore the three main functions of water in concrete: the hydration process, workability, and strength.
Hydration Process
The hydration process is the chemical reaction between water and cement that forms the hardened structure of concrete. When water is added to cement, it initiates a series of reactions that produce compounds such as calcium silicate hydrate (C-S-H) and calcium hydroxide. These compounds are responsible for the hardening and strength of concrete.
During hydration, water molecules penetrate the cement particles, causing them to dissolve and form a gel-like substance. This gel fills the spaces between the aggregates (sand, gravel, or crushed stone), binding them together to form a solid mass. The hydration process continues over time, increasing the strength and durability of the concrete. Proper curing, which involves maintaining adequate moisture levels, is essential to allow the hydration process to proceed effectively and achieve optimal strength.
Workability
Workability refers to the ease with which concrete can be mixed, placed, and finished. Water significantly affects the workability of concrete, making it easier to handle and mold into the desired shape. The right amount of water ensures that the concrete mix is neither too dry nor too wet.
A well-balanced mix will have enough water to coat all the particles and provide lubrication, allowing the mix to flow smoothly. However, adding too much water can lead to segregation, where the aggregates settle at the bottom, and the cement paste rises to the top, resulting in a weak and porous structure. Conversely, too little water can make the mix stiff and difficult to work with, leading to poor compaction and the potential for voids within the concrete.
To achieve the desired workability, the water content must be carefully controlled, considering factors such as the type of cement, aggregates, and admixtures used in the mix.
Strength
The strength and durability of concrete are closely linked to the water-cement ratio, which is the proportion of water to cement in the mix. A lower water-cement ratio generally leads to higher strength and durability, as there is less excess water to evaporate, reducing the formation of pores and voids in the hardened concrete.
For example, a water-cement ratio of 0.4 (40 parts water to 100 parts cement) typically results in high-strength concrete, as there is just enough water to hydrate the cement particles without leaving excess water that can weaken the structure. In contrast, a higher water-cement ratio, such as 0.6, may result in lower strength and durability due to the increased likelihood of pores and cracks forming as the excess water evaporates.
Balancing the water-cement ratio is essential to achieve the desired properties of concrete, ensuring it meets the specific requirements of the project. Factors such as environmental conditions, the intended use of the structure, and the desired lifespan must be considered when determining the appropriate water-cement ratio.
Water is a vital component in the concrete mix, influencing the hydration process, workability, and strength of the final product. Understanding the role of water and carefully controlling the water-cement ratio can help ensure the creation of durable, high-quality concrete structures. Whether you are working on a small residential project or a large-scale commercial development, paying attention to the role of water in concrete can make a significant difference in the long-term performance and reliability of your construction.

Optimal Water-Cement Ratio
Understanding the optimal water-cement ratio is crucial for achieving the desired strength, durability, and workability in concrete projects. This section delves into the standards and guidelines for water-cement ratios in various applications and provides insights on how to adjust the ratio based on specific conditions.
Standards and Guidelines
The water-cement ratio is a key determinant of concrete quality. It refers to the ratio of the weight of water to the weight of cement used in a concrete mix. The ideal ratio varies depending on the type of concrete project and its requirements.
1. Foundations
- For most foundation work, a water-cement ratio of 0.45 to 0.60 is recommended. This range ensures sufficient workability and strength for the concrete to support the structural load.
2. Driveways
- Concrete driveways typically require a slightly lower water-cement ratio, often between 0.40 and 0.50. This range helps achieve a dense, durable surface that can withstand weathering and vehicular traffic.
3. Buildings
- For general building construction, a ratio of 0.40 to 0.50 is usually optimal. This ensures a balance between strength and workability, allowing for easy placement and adequate curing.
These standards provide a guideline for achieving the desired performance in different concrete applications. However, adjustments may be necessary based on specific conditions.
Adjusting the Ratio
The optimal water-cement ratio can vary based on several factors, including environmental conditions and the specific requirements of the project. Here’s how to fine-tune the ratio for various scenarios:
1. Weather Conditions
Hot Weather
- In hot climates, concrete tends to dry out quickly, which can lead to cracking and reduced strength. To counteract this, slightly increasing the water content while ensuring proper curing can help maintain workability and prevent premature drying. However, it’s crucial to avoid adding too much water, as it can compromise the concrete’s strength.
Cold Weather
- In cold conditions, concrete sets more slowly, and excess water can lead to freezing and damage. Using a lower water-cement ratio and incorporating admixtures to accelerate curing can help achieve the desired strength without risking freeze-thaw damage.
2. Project Type
High-Strength Concrete
- For projects requiring high-strength concrete, such as columns and beams in high-rise buildings, a lower water-cement ratio (0.35 to 0.40) is often necessary. This ensures higher density and strength, although it may reduce workability. Superplasticizers can be used to enhance workability without increasing the water content.
Lightweight Concrete
- Lightweight concrete used in non-structural applications or insulation typically benefits from a higher water-cement ratio (0.50 to 0.60). This improves workability and ensures uniform distribution of lightweight aggregates, though care must be taken to balance workability with strength requirements.
3. Workability Needs
- Adjusting the water-cement ratio to meet specific workability requirements is essential. For instance, concrete used in intricate molds or forms may need a higher ratio to ensure it fills all spaces adequately. Conversely, for applications requiring high precision and minimal shrinkage, a lower ratio is preferable.
4. Mix Design Adjustments
- Beyond the water-cement ratio, the mix design can be modified by using supplementary cementitious materials like fly ash, slag, or silica fume. These materials can improve the mix’s properties and allow for adjustments in the water-cement ratio to achieve specific performance criteria.
Understanding and optimizing the water-cement ratio is critical for successful concrete projects. By adhering to standard guidelines and making necessary adjustments based on environmental conditions and project requirements, you can ensure the concrete’s strength, durability, and workability are up to par.

Effects Of Improper Water-Cement Ratios
Achieving the right water-cement ratio is crucial for the integrity and longevity of concrete structures. This balance is essential to ensure that concrete not only sets properly but also reaches its full potential in terms of strength and durability. When the water-cement ratio is not correctly managed, several problems can arise. Below, we delve into the effects of having either too much or too little water in the concrete mix.
Too Much Water
When the water-cement ratio exceeds the recommended level, the following issues can occur:
1. Reduced Strength
- Explanation: Excess water dilutes the cement paste, leading to a weaker bond between the cement particles and the aggregates.
- Impact: This dilution results in a significant reduction in the overall strength of the concrete. Structures made with such concrete are more prone to damage and failure under stress.
2. Increased Permeability:
- Explanation: More water in the mix creates a porous structure with larger capillary voids.
- Impact: Increased permeability allows water and other harmful substances to penetrate the concrete more easily, accelerating the process of deterioration and corrosion of reinforcement bars.
3. Potential for Cracks:
- Explanation: As the concrete sets, the excess water evaporates, leaving behind large voids and shrinkage.
- Impact: These voids can lead to the development of cracks, which not only weaken the structure but also provide pathways for moisture and chemicals to enter, further compromising the concrete’s integrity.
Too Little Water
Conversely, an insufficient water-cement ratio can also be problematic:
1. Poor Workability
- Explanation: Water acts as a lubricant in the concrete mix, facilitating easier handling and placement.
- Impact: Without enough water, the concrete becomes stiff and difficult to work with. This poor workability can lead to improper compaction and finishing, which negatively affects the concrete’s surface quality and uniformity.
2. Incomplete Hydration:
- Explanation: Water is necessary for the chemical reaction that causes cement to set and harden, known as hydration.
- Impact: Insufficient water means not all the cement particles will hydrate, leading to a weaker matrix. This incomplete hydration reduces the concrete’s overall strength and resilience.
3. Reduced Durability:
- Explanation: Proper hydration is critical for forming a strong and durable concrete matrix.
- Impact: With too little water, the concrete fails to develop the desired properties, making it less resistant to environmental stressors such as freeze-thaw cycles, abrasion, and chemical attacks. Over time, this reduced durability can lead to premature deterioration and higher maintenance costs.
In summary, maintaining the correct water-cement ratio is vital for producing high-quality concrete. Both excessive and insufficient water in the mix can lead to a host of problems, compromising the concrete’s strength, permeability, and overall durability. By carefully controlling the water-cement ratio, one can ensure that the concrete achieves the desired performance characteristics, leading to safer and more durable structures.

Measuring And Controlling The Water-Cement Ratio
Tools and Techniques
Measuring and controlling the water-cement ratio (W/C ratio) is vital in achieving the desired properties of concrete. The water-cement ratio is the weight of water to the weight of cement used in a concrete mix. Here are some of the key tools and techniques used on-site to ensure the correct ratio:
1. Concrete Mixers with Built-In Water Meters: Modern concrete mixers often come equipped with water meters that precisely measure the amount of water added to the mix. These meters help ensure that the exact amount of water specified in the mix design is used.
2. Weighing Scales: Accurate digital weighing scales are used to measure the exact amounts of cement and water. This helps in maintaining the precise water-cement ratio required for the concrete mix.
3. Slump Test: The slump test is a simple and widely used method to assess the consistency of the concrete mix. A standard cone-shaped mold is filled with concrete, and the slump (how much the concrete settles) is measured after the mold is lifted. This test provides an indirect measure of the water-cement ratio, as too much water will result in a higher slump.
4. Moisture Probes: These probes are inserted into the aggregate storage areas to measure the moisture content of the aggregates. The moisture content of aggregates can significantly affect the water-cement ratio, and adjusting the water content based on these measurements is crucial.
5. Chemical Admixtures: Chemical admixtures like superplasticizers can be used to adjust the workability of the concrete without altering the water-cement ratio. This allows for the required consistency while maintaining the integrity of the mix.
6. Batching Software: Advanced batching software systems control and monitor the proportions of materials in the concrete mix. These systems ensure that the water-cement ratio is maintained according to the specified mix design.
Quality Control
Maintaining the correct water-cement ratio is essential for quality control in construction. The water-cement ratio directly influences the strength, durability, and overall performance of the concrete. Here are some reasons why this ratio is critical for quality control:
1. Strength: The strength of concrete is inversely proportional to the water-cement ratio. A lower water-cement ratio leads to higher strength and durability. By controlling this ratio, the structural integrity of the building is ensured.
2. Durability: A proper water-cement ratio reduces the permeability of concrete, which in turn increases its resistance to weathering, chemical attack, and other environmental factors. This ensures the longevity of the structure.
3. Workability: The workability of concrete is essential for ease of placement and compaction. While maintaining a low water-cement ratio is important for strength, the mix must still be workable enough to be placed and finished properly. This balance is achieved through precise control and adjustment of the mix.
4. Preventing Cracks: Excess water in the concrete mix can lead to increased shrinkage and cracking as the concrete dries. Controlling the water-cement ratio helps in minimizing these defects, resulting in a smoother, more uniform finish.
5. Consistency: Consistency in the water-cement ratio across different batches of concrete is crucial for uniform quality. Variations in this ratio can lead to differences in strength and durability, which can compromise the structural integrity.
6. Adherence to Standards: Construction projects must adhere to various local and international standards, which specify the acceptable ranges for water-cement ratios. Ensuring compliance with these standards is vital for obtaining necessary approvals and certifications.
By using the right tools and techniques to measure and control the water-cement ratio, construction professionals can ensure the quality and durability of their projects. This attention to detail not only meets regulatory standards but also enhances the overall performance and lifespan of the structures they build.

Real-World Applications And Case Studies
Successful Projects
In the construction industry, numerous projects stand as a testament to the critical importance of the correct water-cement ratio. Take, for example, the Burj Khalifa in Dubai. The world’s tallest building had stringent requirements for its concrete mix to ensure structural integrity and durability. The engineers meticulously controlled the water-cement ratio to produce a high-strength concrete that could withstand the immense pressures at the base of the tower. The success of this project highlights how adherence to the proper water-cement ratio can result in extraordinary achievements in construction.
Another notable project is the Hoover Dam, a marvel of modern engineering completed in the 1930s. The dam’s construction involved the use of 3.25 million cubic yards of concrete. The project’s success relied heavily on maintaining the correct water-cement ratio, ensuring the concrete would set correctly and endure the test of time. Today, nearly a century later, the Hoover Dam continues to operate efficiently, illustrating the long-term benefits of precise water-cement ratio management.
Lessons Learned
While there are shining examples of success, there are also cautionary tales in the construction world where improper water-cement ratios have led to significant issues. One such case is the Civic Center complex in California. Initially constructed in the late 20th century, the complex began showing signs of severe concrete degradation just a few years after completion. Investigations revealed that an improper water-cement ratio had been used during construction, leading to weak concrete that couldn’t withstand environmental stresses. This failure underscored the necessity of strict adherence to correct ratios, ultimately resulting in expensive repairs and a reevaluation of construction practices.
Another instructive example is the collapse of the Skyline Plaza in Virginia in 1973. The primary cause of the collapse was linked to a combination of design flaws and poor concrete quality due to an incorrect water-cement ratio. The disaster, which resulted in significant loss of life and property, served as a grim reminder of the potential consequences of neglecting proper concrete mix proportions. This tragedy led to stricter building codes and regulations, emphasizing the need for accuracy in every aspect of construction.
These real-world examples underline the paramount importance of the water-cement ratio in construction projects. They serve as both inspiration and caution, demonstrating the potential for both extraordinary success and devastating failure based on the attention given to this crucial aspect of concrete mix design. As such, the industry continues to learn and evolve, constantly striving to perfect the balance necessary to create safe, durable, and long-lasting structures.

Innovations And Advances In Concrete Technology
The world of concrete technology is continuously evolving, bringing forth new materials and technological integrations that significantly impact the industry. These advancements are crucial for improving the quality, durability, and sustainability of concrete structures. Here, we delve into the latest innovations and how they influence the critical water-cement ratio, a key factor in concrete performance.
New Materials
One of the most exciting areas of innovation in concrete technology is the development of new materials that enhance the properties of concrete. Researchers and engineers are constantly experimenting with various additives and supplementary cementitious materials (SCMs) to improve concrete’s workability, strength, and environmental footprint.
High-Performance Admixtures: These chemical compounds are added to the concrete mix to improve various properties, including the water-cement ratio. Superplasticizers, for example, allow for a reduction in the water content without compromising workability. This leads to denser, stronger concrete with a lower risk of shrinkage and cracking.
Nanomaterials: The incorporation of nanomaterials, such as nano silica and nano clay, has shown significant promise. These materials can refine the microstructure of concrete, enhancing its mechanical properties and durability. By improving the hydration process, they help achieve a more efficient water-cement ratio, resulting in a stronger and more durable final product.
Recycled Materials: The use of recycled aggregates and industrial by-products, such as fly ash, slag, and silica fume, is becoming increasingly popular. These materials not only reduce the environmental impact of concrete production but also improve the performance characteristics of the mix. For instance, fly ash can improve the workability and strength of concrete, allowing for a more optimized water-cement ratio.
Technology Integration
Modern technology plays a pivotal role in maintaining the optimal water-cement ratio in concrete production. The integration of advanced technologies ensures precision, efficiency, and consistency in concrete mixes, leading to superior quality and performance.
Artificial Intelligence (AI): AI and machine learning algorithms are revolutionizing the concrete industry. These technologies can analyze vast amounts of data from past projects to predict the optimal mix design for specific conditions. By considering factors such as temperature, humidity, and material properties, AI helps in achieving the perfect water-cement ratio, enhancing the overall quality and durability of concrete structures.
Smart Sensors: The use of smart sensors in concrete production and curing processes allows for real-time monitoring of various parameters, including moisture levels, temperature, and hydration progress. These sensors provide critical data that can be used to adjust the mix design on the fly, ensuring the ideal water-cement ratio is maintained throughout the process. This leads to better control over the curing process, resulting in concrete with optimal strength and durability.
3D Printing: The advent of 3D printing in the construction industry has opened new avenues for concrete technology. 3D printing allows for precise control over the mix and placement of concrete, ensuring a consistent water-cement ratio throughout the structure. This technology reduces waste, improves construction speed, and enhances the quality of the final product.
Automated Batching Systems: Automated batching systems ensure that the exact proportions of water, cement, and aggregates are mixed together consistently. These systems reduce human error and variability in the mixing process, leading to a more precise water-cement ratio and, consequently, higher-quality concrete.
The continuous advancements in concrete technology, particularly in the development of new materials and the integration of modern technology, are transforming the industry. These innovations not only enhance the properties and performance of concrete but also ensure a more efficient and sustainable construction process. By optimizing the critical water-cement ratio, these advancements contribute to the creation of stronger, more durable, and environmentally friendly concrete structures, paving the way for a more resilient built environment.
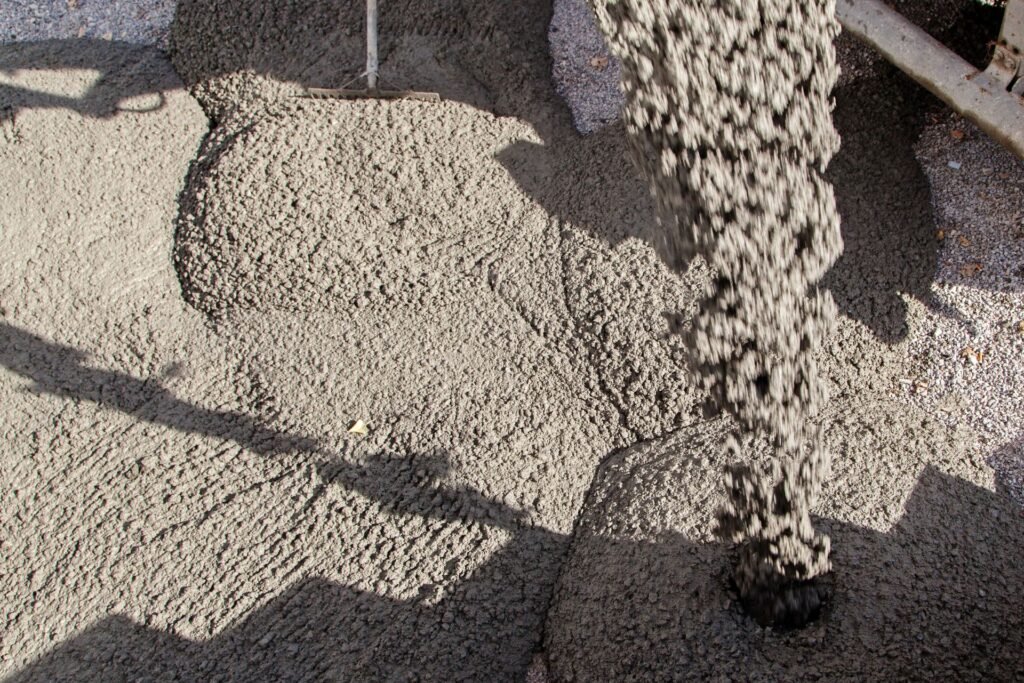
Practical Tips For Contractors And DIY Enthusiasts
Ensuring the right water-cement ratio is crucial for achieving optimal concrete strength and durability. Here are some practical tips to help both contractors and DIY enthusiasts.
Best Practices
1. Measure Accurately: Always measure the water and cement precisely. Using too much water can weaken the concrete, while too little can make it difficult to work with.
2. Use a Consistent Mix: Ensure the mix is consistent for every batch. Variability can lead to differences in strength and finish.
3. Understand the Environment: The water-cement ratio may need adjustment based on environmental conditions. For instance, hot and dry climates may require more water to prevent the mix from drying out too quickly.
4. Employ Admixtures Wisely: Use admixtures like plasticizers to improve workability without altering the water-cement ratio. These can help in achieving the desired consistency and strength.
5. Cure Properly: Proper curing is vital for the hydration process. Ensure the concrete is kept moist for at least 7 days to achieve maximum strength.
6. Test Regularly: Conduct slump tests and other checks to ensure the mix meets the required standards. Regular testing helps in maintaining consistency and quality.
Common Mistakes to Avoid
1. Overwatering the Mix: One of the most common mistakes is adding too much water to make the mix easier to work with. This can significantly reduce the concrete’s strength.
2. Ignoring the Mix Ratios: Sometimes, in a rush, exact ratios are ignored. This can lead to poor-quality concrete that may not meet structural requirements.
3. Poor Mixing: Failing to mix the components thoroughly can result in weak spots within the concrete. Ensure the mixture is homogeneous.
4. Not Accounting for Aggregate Moisture: Aggregates can contain moisture that affects the overall water content of the mix. Always consider this moisture when calculating the water-cement ratio.
5. Incorrect Use of Admixtures: Misusing admixtures or not following manufacturer guidelines can lead to unintended consequences. Always follow the recommended dosages and procedures.
6. Inadequate Curing: Neglecting the curing process can prevent the concrete from reaching its full strength. Ensure the concrete is properly cured to avoid cracks and other issues.
By following these best practices and avoiding common mistakes, you can ensure that your concrete projects are strong, durable, and long-lasting. Whether you’re a seasoned contractor or a DIY enthusiast, these tips will help you achieve professional results.

FAQs: About Why Is The Science Of the Water-Cement Ratio So Critical
What is the water-cement ratio?
The water-cement ratio is the ratio of the weight of water to the weight of cement used in a concrete mix. This ratio is crucial in determining the strength and durability of the concrete.
Why is the water-cement ratio important?
The water-cement ratio is important because it affects the hydration process of cement, which in turn influences the strength, durability, and workability of the concrete. An optimal ratio ensures that the concrete has the desired properties for its intended use.
How does the water-cement ratio affect concrete strength?
A lower water-cement ratio leads to higher concrete strength and durability because there is less excess water in the mix, resulting in a denser and more compact structure. Conversely, a higher ratio can weaken the concrete, making it more susceptible to cracks and damage.
What is the optimal water-cement ratio for most concrete mixes?
The optimal water-cement ratio typically ranges from 0.4 to 0.6, depending on the specific requirements of the concrete project. Lower ratios are used for high-strength concrete, while higher ratios may be suitable for concrete with less stringent strength requirements.
What problems can arise from an incorrect water-cement ratio?
Incorrect water-cement ratios can lead to various issues. Too much water can cause the concrete to be weak, porous, and prone to cracking. Too little water can result in poor workability, incomplete hydration, and reduced strength and durability.
How can the water-cement ratio be measured and controlled?
The water-cement ratio can be measured by weighing the water and cement used in the mix. Controlling the ratio involves careful measurement and mixing, often using tools and techniques such as moisture meters and precise batching methods to ensure consistency.
Are there any tools or technologies that help maintain the correct water-cement ratio?
Yes, modern construction practices often employ tools and technologies like moisture meters, batch controllers, and AI-driven systems to accurately measure and control the water-cement ratio, ensuring optimal concrete quality.
How does the water-cement ratio impact concrete workability?
The water-cement ratio directly affects the workability of concrete. A higher ratio makes the mix more fluid and easier to work with, while a lower ratio results in a stiffer mix that can be more challenging to place and finish.
Can the water-cement ratio be adjusted on-site?
Yes, the water-cement ratio can be adjusted on-site by adding water or cement to the mix. However, any adjustments should be made with caution and precision to avoid compromising the concrete’s properties.
What are some best practices for ensuring the correct water-cement ratio?
Best practices for ensuring the correct water-cement ratio include precise measurement of ingredients, consistent mixing procedures, regular quality checks, and the use of modern technologies to monitor and adjust the ratio as needed. Following these practices helps achieve high-quality, durable concrete.
Conclusion
In conclusion, it’s essential to recap the key points discussed about the water-cement ratio and its pivotal role in concrete science. This ratio significantly impacts the strength, durability, and overall performance of concrete, making it a critical factor for any construction project. Understanding the science behind the water-cement ratio helps ensure that concrete structures are robust and long-lasting. As we’ve explored, maintaining the correct balance between water and cement can prevent issues like cracking and weakening, which are common in improperly mixed concrete. We encourage you to share your experiences or ask questions about your concrete projects in the comments below. Your insights and inquiries not only contribute to the community but also help others facing similar challenges.
About the Author:
Mike Veail is a recognized digital marketing expert with over 6 years of experience in helping tradespeople and small businesses thrive online. A former quantity surveyor, Mike combines deep industry knowledge with hands-on expertise in SEO and Google Ads. His marketing strategies are tailored to the specific needs of the trades sector, helping businesses increase visibility and generate more leads through proven, ethical methods.
Mike has successfully partnered with numerous companies, establishing a track record of delivering measurable results. His work has been featured across various platforms that showcase his expertise in lead generation and online marketing for the trades sector.
Learn more about Mike's experience and services at https://theleadguy.online or follow him on social media: